Design and build of the 3D Printing Gantry with a single bridge and a vertical beam with the advanced print nozzle
Customer: One COMPOSITES
Segment: Large scale 3D printers
Project: VSF Gantry Printing and
Milling and Robotic Spraying
#11-2 Design and build of the 3D Printing Gantry with a single bridge and a vertical beam with the advanced print nozzle
Customer: One COMPOSITES
Segment: Large scale 3D printers
Project: VSF Gantry Printing and
Milling and Robotic Spraying
The Customer
Queensland manufacturer One Composites, a
fully owned subsidiary of Zone RV, where their
VSF-3D printing system is the largest in the
Southern Hemisphere. The 22m x 5m x 1.6m
system was initially established for both 3D
printing and machining in composite materials for
a wide range of off-road caravans that combine
lightweight composite bodies with lass-leading
components.
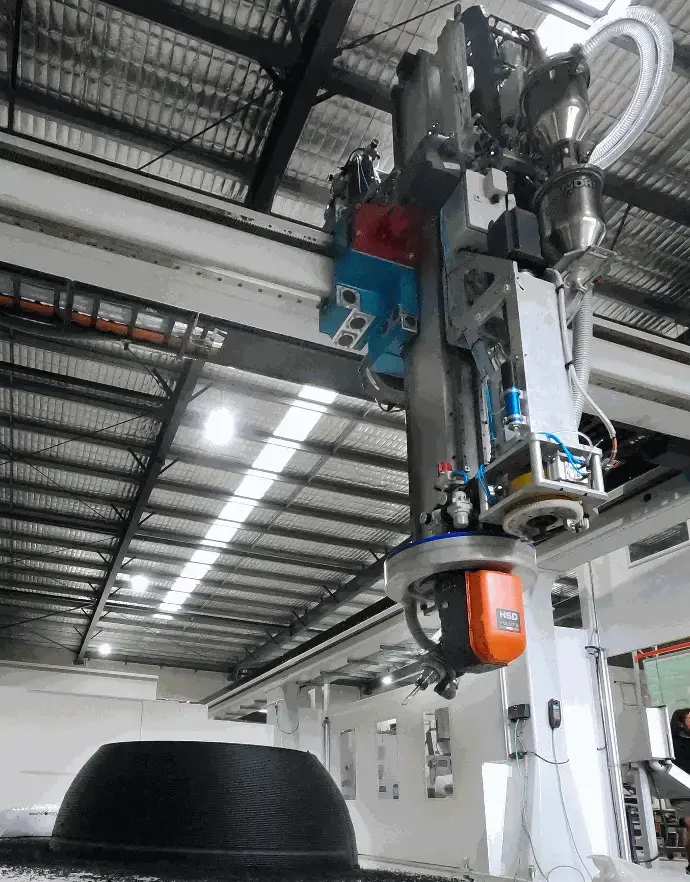
Why CNC Design?
CNC Design, an established Australian company
with core competencies in Machine Tools,
Engineered Drives, Robotics, and Additive
technologies, has recently commissioned a new
range of large-scale additive VSF-3D printers.
These thermoplastic composite printers have the
potential to revolutionise the manufacturing
industry by enabling the production of a wide
range of items such as plugs, moulds, fixtures,
structural components, formwork, decorative
pieces, and architectural parts.
The Equipment
At One Composites CNC Design's Virtual Smart Factory (VSF) platform stands at the forefront of Industry 4.0, representing a digital robotic system that harnesses the power of standard modular and versatile components. Tailored for additive, machining, and handling applications, VSF is a robust solution that redefines manufacturing processes.
At its core, VSF is propelled by the SIEMENS
SINUMERIK ONE CNC system, offering distinct
advantages over conventional Robot controllers
with its exceptional path accuracy and a
user-friendly standard CNC G Code programming
interface. Adding to its capabilities, the integration
of the HSD HS673 2-axis milling head, affixed to
the Z-axis vertical beam, ensures precision and
efficiency in high-speed 5-axis milling operations
for composites, wood, and plastics.
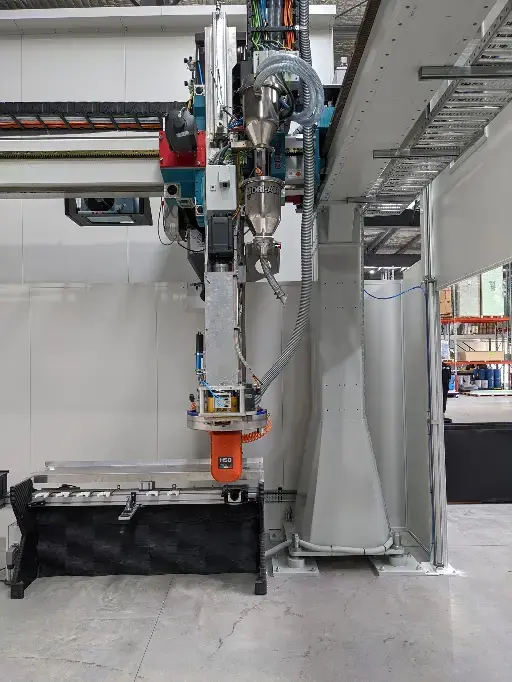
Why CNC Design?
CNC Design, an established Australian company
with core competencies in Machine Tools,
Engineered Drives, Robotics, and Additive
technologies, has recently commissioned a new
range of large-scale additive VSF-3D printers.
These thermoplastic composite printers have the
potential to revolutionise the manufacturing
industry by enabling the production of a wide
range of items such as plugs, moulds, fixtures,
structural components, formwork, decorative
pieces, and architectural parts.
The Equipment
At One Composites CNC Design's Virtual Smart Factory (VSF) platform stands at the forefront of Industry 4.0, representing a digital robotic system that harnesses the power of standard modular and versatile components. Tailored for additive, machining, and handling applications, VSF is a robust solution that redefines manufacturing processes.
At its core, VSF is propelled by the SIEMENS
SINUMERIK ONE CNC system, offering distinct
advantages over conventional Robot controllers
with its exceptional path accuracy and a
user-friendly standard CNC G Code programming
interface. Adding to its capabilities, the integration
of the HSD HS673 2-axis milling head, affixed to
the Z-axis vertical beam, ensures precision and
efficiency in high-speed 5-axis milling operations
for composites, wood, and plastics.
Application Centre
This new facility is supporting One Composites
and other clients in the development and testing
of INNOMERIX's new advanced materials that
are specifically formulated for large scale printing
and machining. The application centre includes
highly specified VSF-3D printer, with a print area
of 12m x 5m x 1.6m, integrated on the same site
as INNOMERIX. Having in-house testing
laboratory, ensures that material properties and
performance can be tested, logged and retained
for customer's and future reference. The centre
also supports VSF-3D sales demonstrations, and
production of specialty components on a
commercial basis.
Design Overview
The VSF-3D printer uses a large area gantry to
carry a patented multi zone extruder for melting
and extrusion, providing the ability to rapidly print
large structures with reinforced composites up to
150kg/hr. In addition, the printers offer an optional
5-axis machining head can provide smooth
surface finishes.
The printers have several other features,
including a nozzle rotation unit with a
temperature-controlled roller to flatten and
compress print bead, a vacuum pellet drying and
conveying system with high performance and
energy efficiency for continuous printing, axis print
speeds up to 20 m/min with axis rapid speeds up
to 60 m/min, changeable nozzles, and Siemens
SINUMERIK ONE controls, the leading platform
for advanced manufacturing.
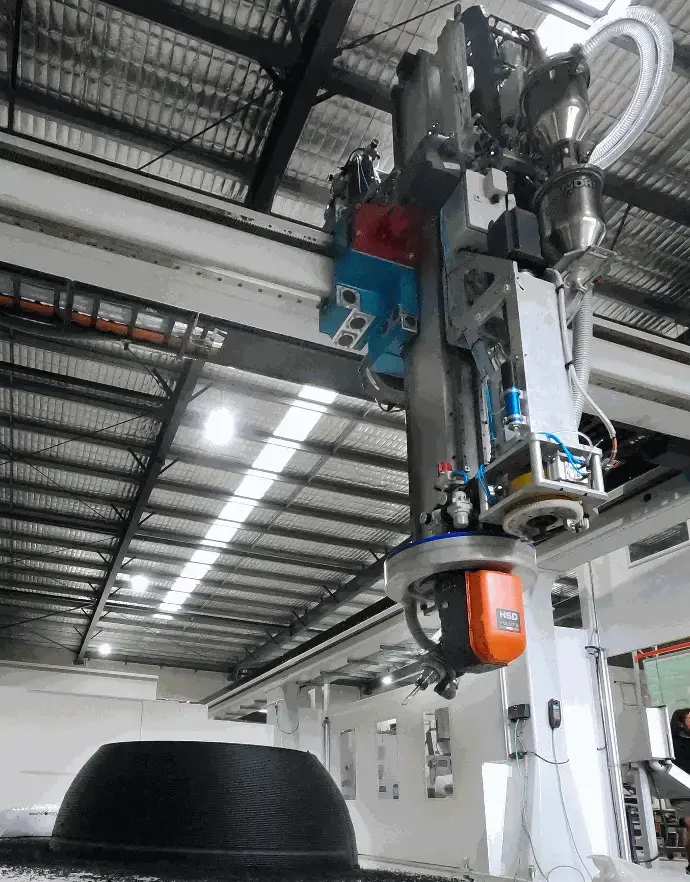
Application Centre
This new facility is supporting One Composites and other clients in the development and testing of INNOMERIX's new advanced materials that are specifically formulated for large scale printing and machining. The application centre includes highly specified VSF-3D printer, with a print area of 12m x 5m x 1.6m, integrated on the same site as INNOMERIX. Having in-house testing laboratory, ensures that material properties and performance can be tested, logged and retained for customer's and future reference. The centre also supports VSF-3D sales demonstrations, and production of specialty components on a commercial basis.
Design Overview
The VSF-3D printer uses a large area gantry to
carry a patented multi zone extruder for melting
and extrusion, providing the ability to rapidly print
large structures with reinforced composites up to
150kg/hr. In addition, the printers offer an optional
5-axis machining head can provide smooth
surface finishes.
The printers have several other features,
including a nozzle rotation unit with a
temperature-controlled roller to flatten and
compress print bead, a vacuum pellet drying and
conveying system with high performance and
energy efficiency for continuous printing, axis print
speeds up to 20 m/min with axis rapid speeds up
to 60 m/min, changeable nozzles, and Siemens
SINUMERIK ONE controls, the leading platform
for advanced manufacturing.
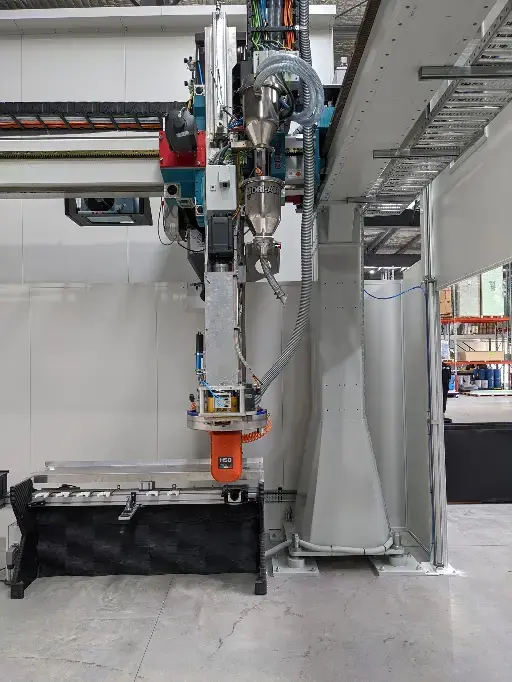
Material Supply and Development
INNOMERIX PTY LTD, a CNC Design subsidiary business, has been established to supply a wide range of thermoplastic composites and currently supplies One Composites. Equipped with a sophisticated compounding line and advanced dosing systems for powder and fibre incorporation into the polymers. This allows material properties such as strength, pliability, impact resistance to be adapted for each application. Other properties such as UV protection, low flammability, and biocides to avoid marine growth can also be added as part of the manufacturing process.
The Result
One Composites CTO, Dave Biggar, says
Whilst investing in new advanced manufacturing technology may be perceived as a high risk, our experienced team quickly mastered the technology and identified a growing demand for large-scale 3D printed and/or machined components. The implementation of this technology has significantly increased our efficiency and versatility, enabling us to combine external project work with initial lightweight composite body production. As a result, our equipment is now being fully utilised, creating a need for additional production capacity and growth in our One Composites business.
Material Supply and Development
INNOMERIX PTY LTD, a CNC Design subsidiary business, has been established to supply a wide range of thermoplastic composites and currently supplies One Composites. Equipped with a sophisticated compounding line and advanced dosing systems for powder and fibre incorporation into the polymers. This allows material properties such as strength, pliability, impact resistance to be adapted for each application. Other properties such as UV protection, low flammability, and biocides to avoid marine growth can also be added as part of the manufacturing process.
The Result
One Composites CTO, Dave Biggar, says
Whilst investing in new advanced manufacturing technology may be perceived as a high risk, our experienced team quickly mastered the technology and identified a growing demand for large-scale 3D printed and/or machined components. The implementation of this technology has significantly increased our efficiency and versatility, enabling us to combine external project work with initial lightweight composite body production. As a result, our equipment is now being fully utilised, creating a need for additional production capacity and growth in our One Composites business.